ZAMM Investments Factory Tour
About ZAMM Investments
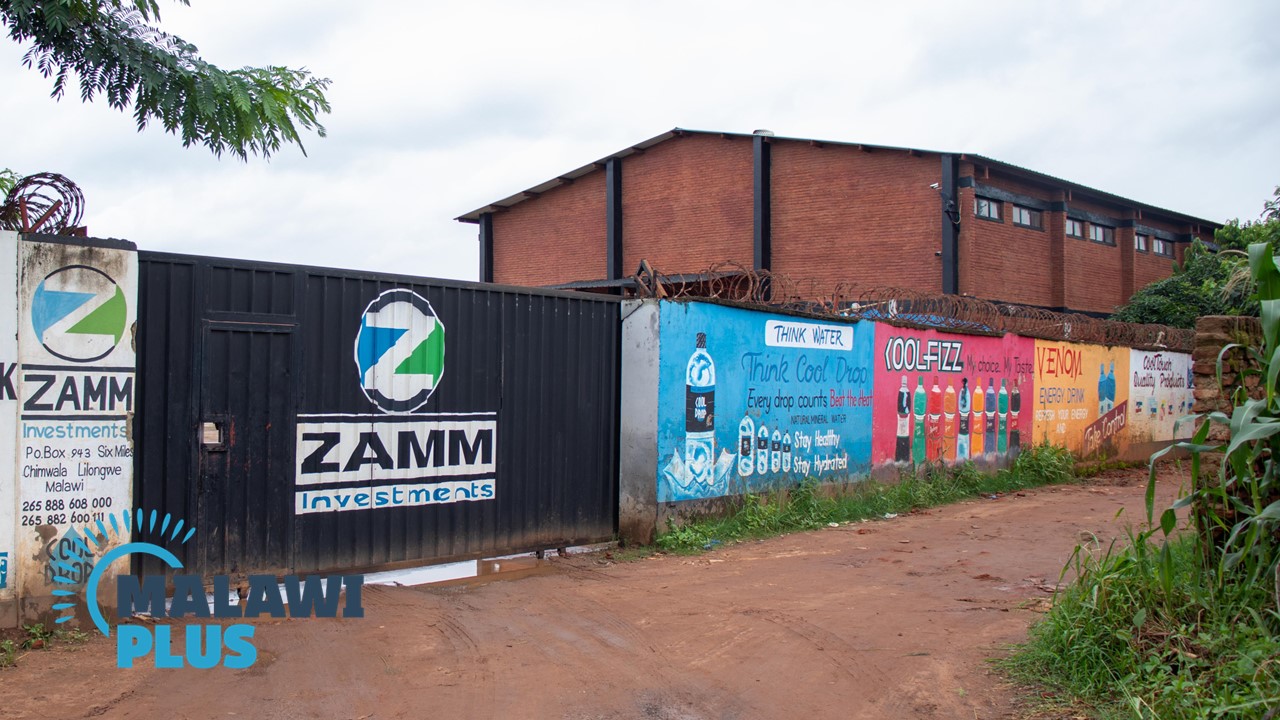
Establishment | 2016 |
---|---|
Total Number of Staff | 320 (Full Time) and 80 (Temporary) As of March 2023 |
Managing Director | Zakariya Tutla |
Address | Six Miles, Lilongwe, Malawi |
Phone | +265 (0) 882 600 111 |
zamminvestments@yahoo.com | |
Website | https://zamminvestments.com |
Zamm Investments is a manufacturing company located at six miles, Lilongwe.
The multi-product company was established in 2016.
The company specialises in the sale and production of purified still water, carbonated beverages, as well as pure and recycled tissue.
Their most popular product is Cool Drop bottled water.
The company was the first to introduce sports caps on water bottles in the country.
They were also the first in Malawi to produce bottled water with seals on the cap.
ZAMM Investments Products
1. Cool Fizz (Orange, Cream Soda, Lime, Ginger, Grape, Rasberry and Cola)
2. Cool Touch Toilet Paper
3. Cool Drop (300ml, 500ml, 750ml, 1L, 2L, 5L and 20L)
Factory Tour
“We adhere to a strict quality control system in every stage of our operation process with a view to ensuring the highest quality standard.“
Bottle Manufacturing Stage
Stage 1 Injection Moulding
Resin is the raw material used to make plastic bottles.
The resins are injected into the machine and get melted. They get processed in the machine into pre-moulds.
Stage 2 Blowing Machine
Here the pre-moulds are heated in the machine into the shape of a bottle.
Different bottles are heated at different temperatures.
The machine automatically picks up the blown bottles and puts them on the conveyor.
Processing & Packaging Stage
Stage 1 Borehole
The borehole has an electric submersible pump that harvests water for processing.
There are six boreholes at this factory.
This borehole is 160 metres deep but some boreholes are as deep as 310 metres.
The boreholes are this deep to ensure a high water yield.
Stage 2 Storage Tanks
This is where the water gets stored when it gets pumped from all six boreholes.
Stage 3 Filtration
From the tanks, the water goes through a rigorous filtration process.
The process starts with sand filtration to filter any sand particles in the water.
Thereafter, the water goes through carbon filtration where certain organic chemicals are removed from the water and also where odours are removed.
Then, the water goes through the softener where ions that make the water to be hard are removed.
After the softener, the water goes through the micron membrane where debris and other microscopic materials are filtered.
From there, it goes into further filtration processes of Sand, carbon, UV treatment, and the micron membrane.
Stage 4 Washing, Rinsing and Loading Machine
The bottles are washed here thoroughly to remove any foreign particles.
Pure water is filled into the washed bottles and caps are fitted on the bottle by the machine as well.
Stage 5 Washing, Rinsing and Loading Machine
The bottles move on a conveyor where three people place labels on the bottles.
Stage 6 Foreign Material Checking
The bottles go through a beam of light where a person checks if there is any foreign material in the water.
This is just a precautionary measure in case the machines missed anything.
If there is any defect in the bottle, the bottle is thrown away.
If three or four bottles with defects are found in a row, the person informs the supervisor to stop the machine so that it can be checked to ensure proper filtration.
The person on this station is changed every hour so that they don’t doze, ensuring quality output.
As the bottles move forward on the conveyor, another person checks the bottles again in case the first person missed something.
Stage 7 Date Printer
As a requirement by authorities, this is where the printer prints the manufacturing date, best-before date, and batch number.
Stage 8 Cap Sealing Machine
The machine places seals on the bottle caps.
This is done deliberately to deal with counterfeit products on the market.
Stage 9 Case Packaging
The bottles continue to move on the conveyor to the bottle-packing machine.
The machine automatically counts the number of bottles required in one case and bundles them in wrapping paper.
Stage 10 The Water Bottles Are Ready for the Market.
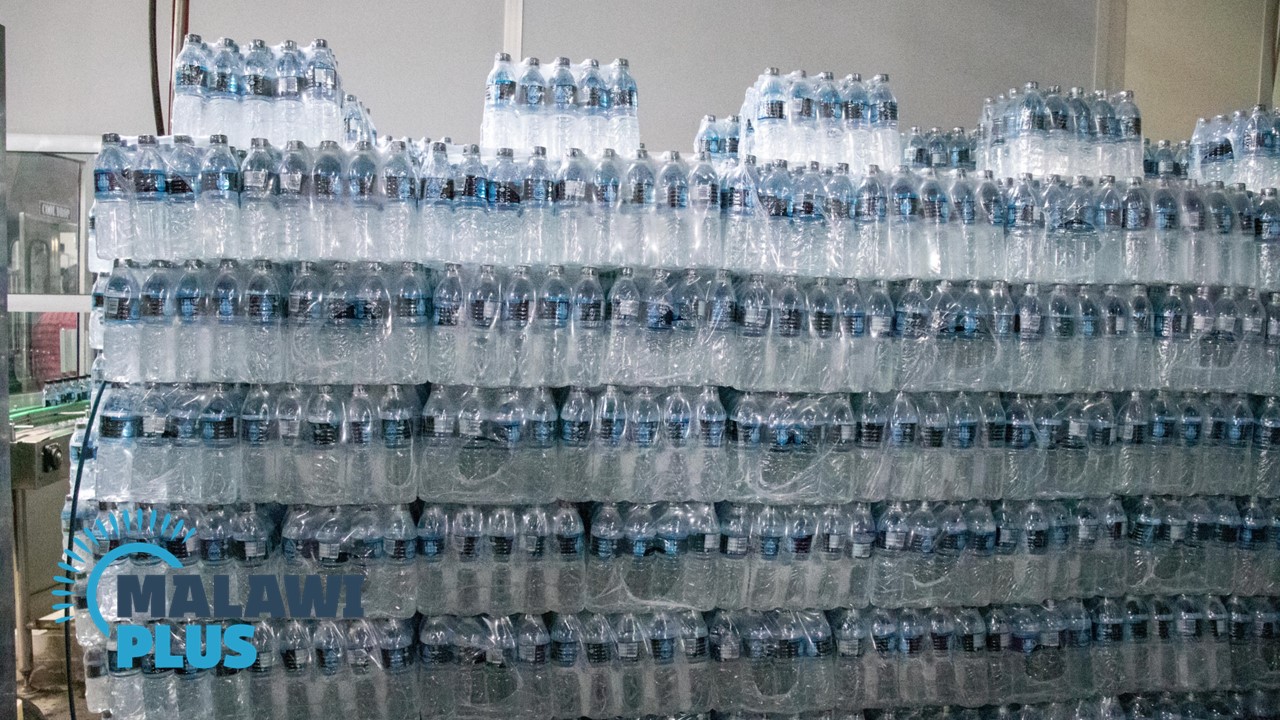